Below are several examples of various kinds of work our unique deburring and chamfering machine systems can perform.
Chamfering Machines Used for Compressor Rotors
Compressor rotors present a huge challenge for deburring. The incredibly tight tolerances on the faces and the seal surfaces require very focused deburring. It also means that using any kind of tool that creates a secondary burr is not going to work. So, milling the chamfer or using any kind of grinding wheel that creates a secondary burr is out of the question. Also, anything that alters the surface finish on the compressor scrolls or ends is not gonna do it.
We used a two-tool MAX System to process these parts. The complex nature of this part required nearly 60 different angles across the two tools. As you can see from the before and after photo, the hanging burrs have been removed and the surface finish was not compromised in any way. Our cycle time to process both ends was 42-seconds.
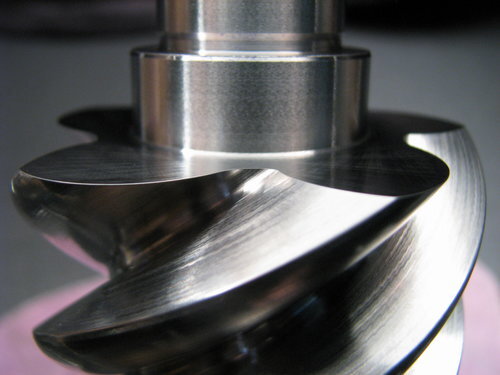
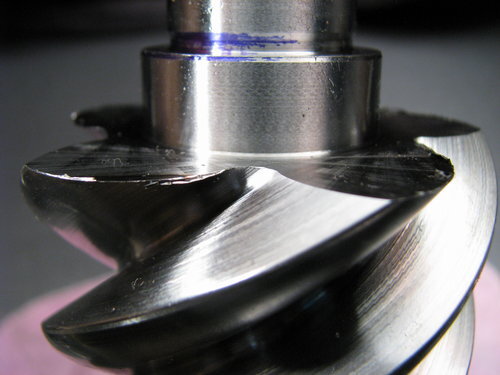
Machine Deburring Jet Engine Turbine Blades
Our machines have the ability to create any size of radius anywhere, including multiple, different radius sizes on different features.
In this example, the titanium-aluminide blades required an extremely uniform radius on all of the features. In addition, a true full-radius was needed, which is extremely hard to do. We have developed very specialized, patented technology that allows us to create the desired radius on the features, while also making them a true full-radius. As you can see from the photos, our result the optimal method. Our cycle time for both ends of the blades, and the length of the blade was 90-seconds.
Machine Deburring Spur Gears - Class 6 Medium Duty Trucks
This is a great example of our superior finish. In this case, we deburred and chamfered both sides of an eight (8) inch spur gear simultaneously. We are the only company that can produce a chamfer this consistent and uniform with a grinding wheel. And we are the ONLY company that can do it in 11-seconds, total.
Deburring and Chamfering Machines for Wind Mills
The 62-inch part pictured is an internal spur gear for the wind industry. It features a chamfer that was intentionally designed to be .040” in the root and .140” on the tip of the tooth. The chamfer we created is completely free of any chatter or striations; it is glass smooth. It also does not have any sharp edges or secondary burrs of any kind. Our machine chamfered both sides in one operation without flipping the part. The cycle time to do both side of this part was 2-minutes.
Patented Deburring System Chamfering Machine for Sprockets
Sprockets can pose a several new challenges. Most, if not all, sprockets have a large tapered end heading to the end of the tooth. They also usually have a large exit burrs. This means that traditional chamfering machines need to create an excessively large chamfer to cope with the tapered end. The excessive chamfer dramatically reduces the strength of the tooth. Our process does not require an excessive chamfer, can cope with the taper, and is fast! Our cycle time on a 12 inch part is 30 seconds.